Should we question the reparability of new buildings?
Author: Stephen MacDougall, P.Eng.
Although a lot of things in our lives are disposable and tend to get replaced when they break, buildings cannot simply be replaced when there is a problem, we need to be able to fix them. The need and ability to repair buildings has always existed and we at Brown & Beattie have built an entire business around how best to plan for and complete the repairs that are a normal part of a building’s life.
But what if it were no longer cost effective to repair a building, would we just throw them away like an old cell phone? In recent years the construction industry has continued to move towards higher performance/lower cost assemblies by using new construction materials and techniques; however, these assemblies may have hidden future costs when it comes time to repair them.
Leakage along with a laundry list of other construction deficiencies were recently identified on the roof of a less than 10-year-old multi-storey residential building. The roof of the building includes a single-ply Thermoplastic Polyolefin (TPO) roofing membrane installed over top of polyisocyanurate board insulation. The TPO roofing membrane is secured to the insulation boards with adhesive and the insulation is attached to the oriented strand board (OSB) wood roof sheathing with mechanical fasteners. The roof sheathing is supported by prefabricated wood trusses and R31 spray foam insulation has been applied to the underside of the sheathing. This is an ‘unvented’ roof assembly, such that there are no provisions for drying out moisture (such as from condensation) which enters the roof assembly.
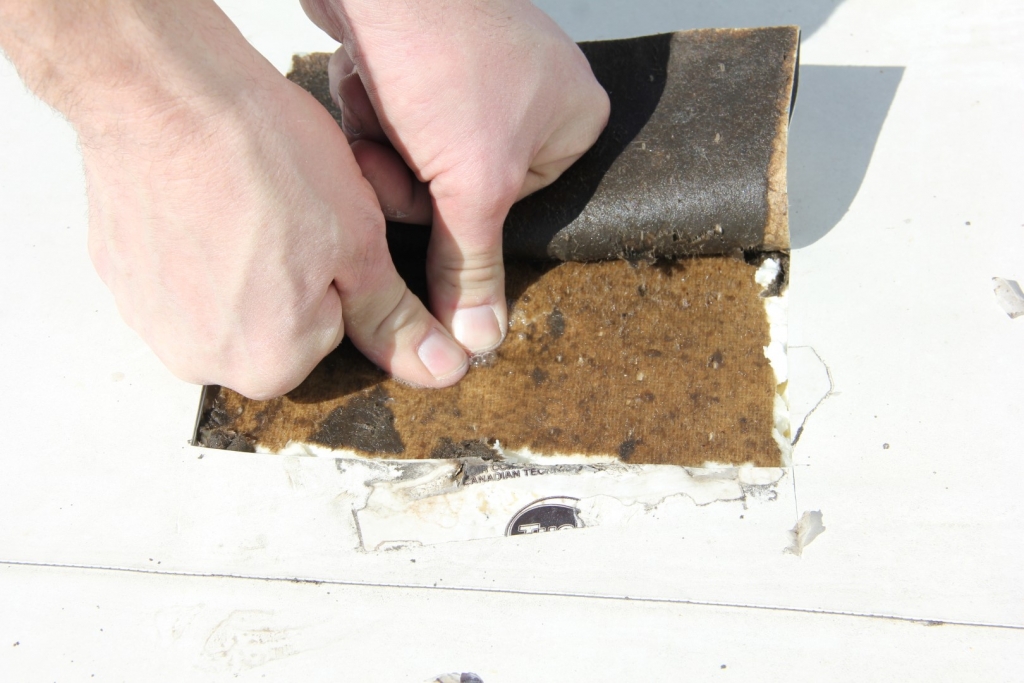
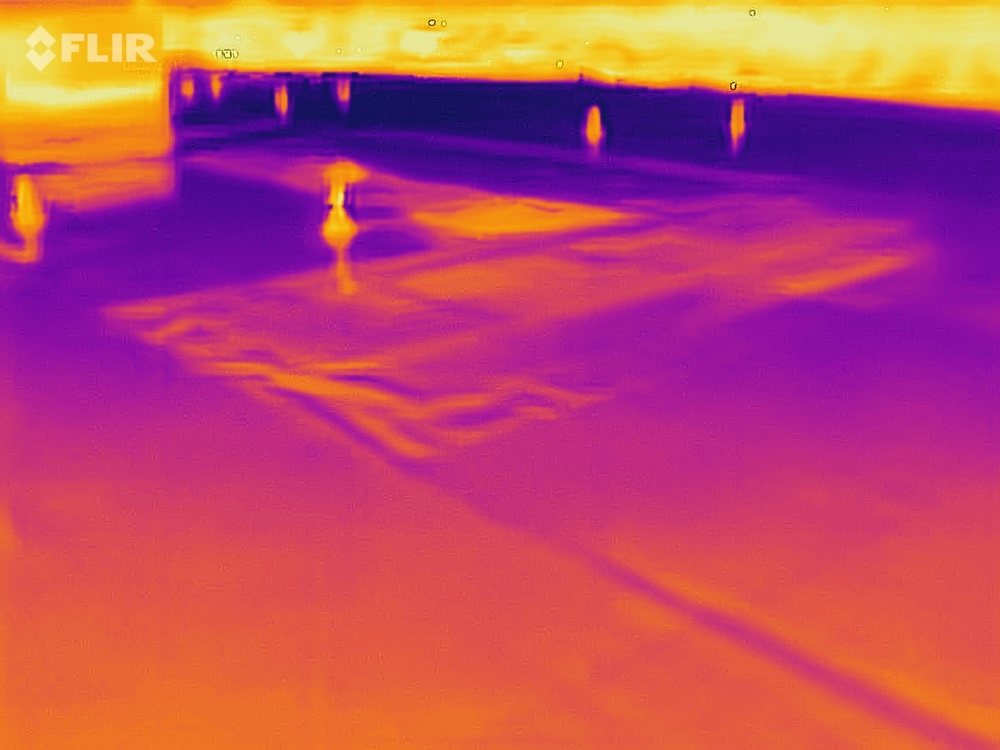
Evidence of leakage within the building had not been reported, however, punctures in the roofing membrane were noted in several locations and thermal scanning indicated that wet insulation was present in various areas throughout the roof. Test cuts through the membrane ultimately confirmed that leakage was occurring and the insulation on top of the sheathing was saturated.
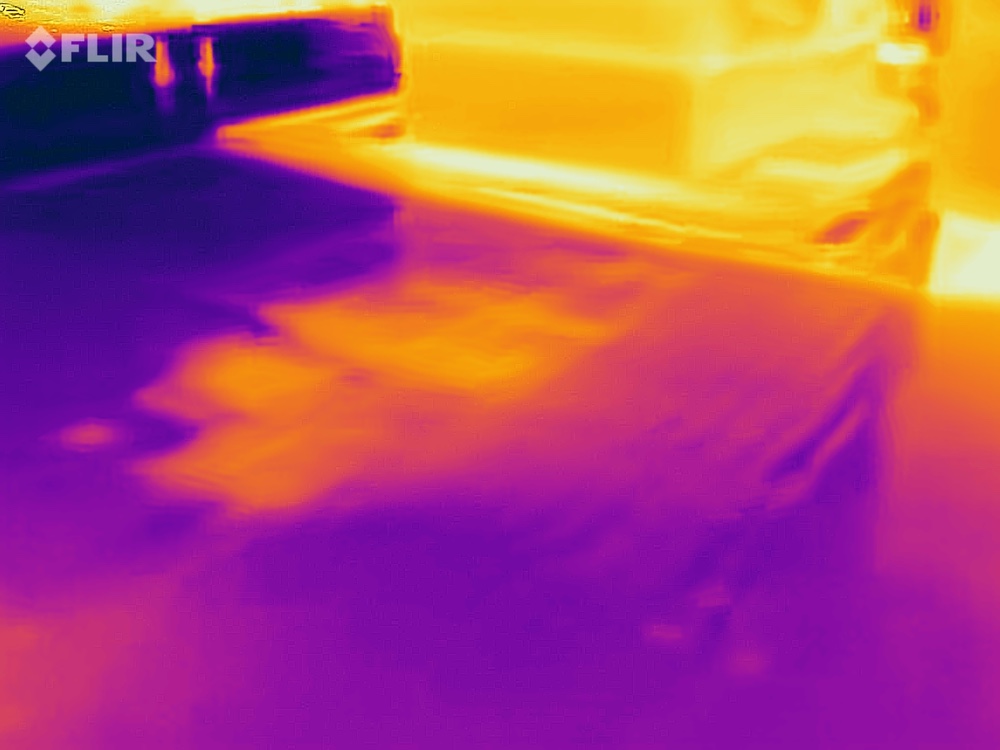
In addition to the wet insulation identified above the roof sheathing, at least portions of the underlying OSB roof sheathing were also wet, the extent of which will need to be confirmed when the roofing is removed. Similarly, the underlying spray foam insulation may also be wet and will also need to be reviewed when the roofing is removed. Due to the adhesive properties of the spray foam, it is likely that at least the top side layers of spray foam will be damaged during the removal of the wet sheathing. In our experience, it is not feasible to dry the sheathing or insulation in place and all of the wet materials will need to be removed.
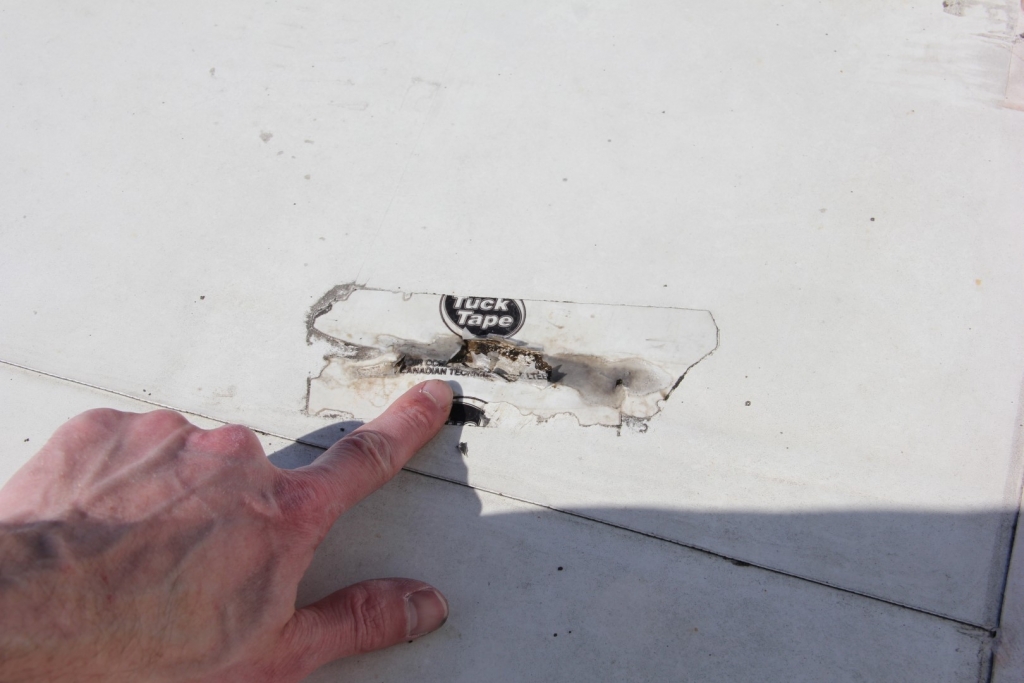
Where the spray foam insulation is damaged when the sheathing is removed, a void will be formed between the foam and new sheathing. The remaining foam is also likely to be cracked, creating discontinuities in the foam’s air/vapour barrier. The presence of these cracks and voids may allow relatively warm and humid air from within the building to come in contact with the underside of the roof sheathing. This creates a risk for condensation to form and result in future moisture related performance issues within the roof assembly. It may be possible to provide ‘breather’ type roof vents in an effort to help limit the build-up of condensation related moisture within these void areas where the sheathing replacements are localized, however, the functionality of these vents for this application would be limited in our experience.
Alternatively, it may be possible to attempt to fill voids in the damaged spray foam with canned spray foam from the top side just prior to the installation of the new sheathing. However, it would be difficult to apply the correct amount of foam to eliminate the voids while not overfilling the space and resulting in damage as the foam expands as it cures. Remaining voids in the foam would also be concealed and not readily identifiable once the sheathing was in place. Spray foam could also be reapplied from the underside of the roof deck in the event areas of the spray foam need to be completely removed. However, this approach would of course require large areas of the ceiling to be removed and would be extremely disruptive to the residents of the building.
In the event large areas of the roof sheathing and underlying spray foam need to be removed, the spray foam could be completely removed and the insulation relocated to above the roof sheathing to form a more conventional roof assembly. As part of this work, a new air/vapour barrier would need to be applied to the top side of the roof sheathing and special care would need to be taken at the transition between the remaining spray foam at the perimeter of the roof to ensure continuous air/thermal/vapour barriers between the new and existing assemblies. The installation of additional insulation above the roof sheathing would of course require the roofing membrane to be completely replaced and would not be suitable for localized repairs.
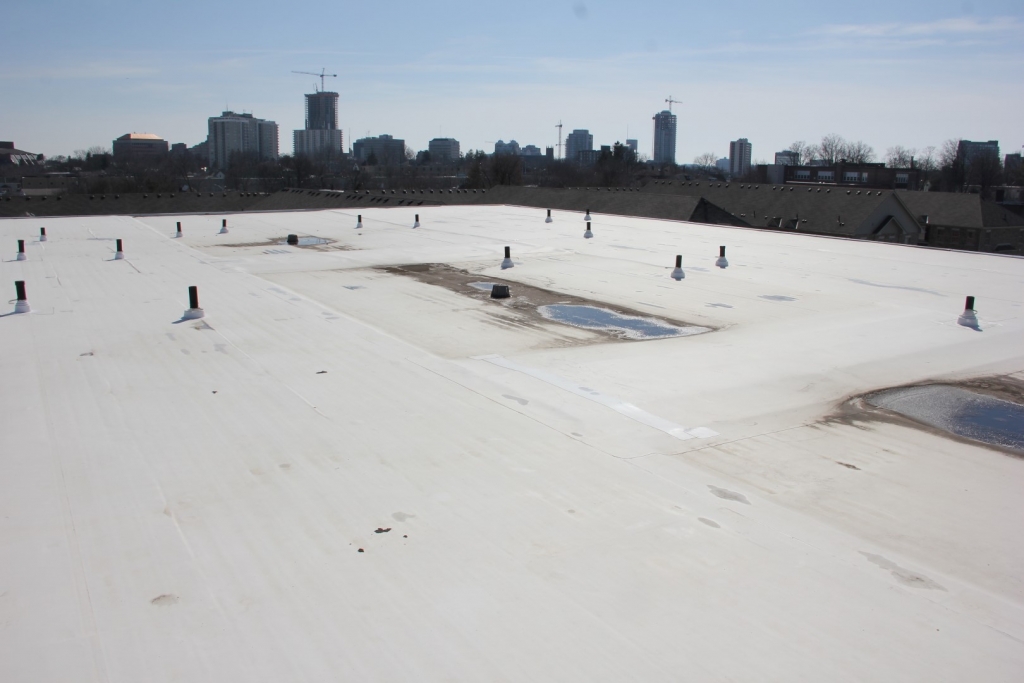
In addition to the water damage to the roof insulation, due to the moisture barrier provided by the spray foam on the underside of the roof deck, the foam may be acting to retain the leakage water around the top of the roof trusses. While the foam may have limited leakage into the building, it helped to conceal the extent of leakage, allowing it to occur possibly over several years. Long-term moisture exposure to the wood trusses as a result of the leakage can result in significant deterioration of the wood and corrosion of the steel truss plates which is a potential structural concern. The condition of these trusses will need to be confirmed when the wet roof sheathing is removed; however, in the event structural deterioration of the roof trusses has occurred, the scope of the repairs may be substantially greater than a simple roofing repair.
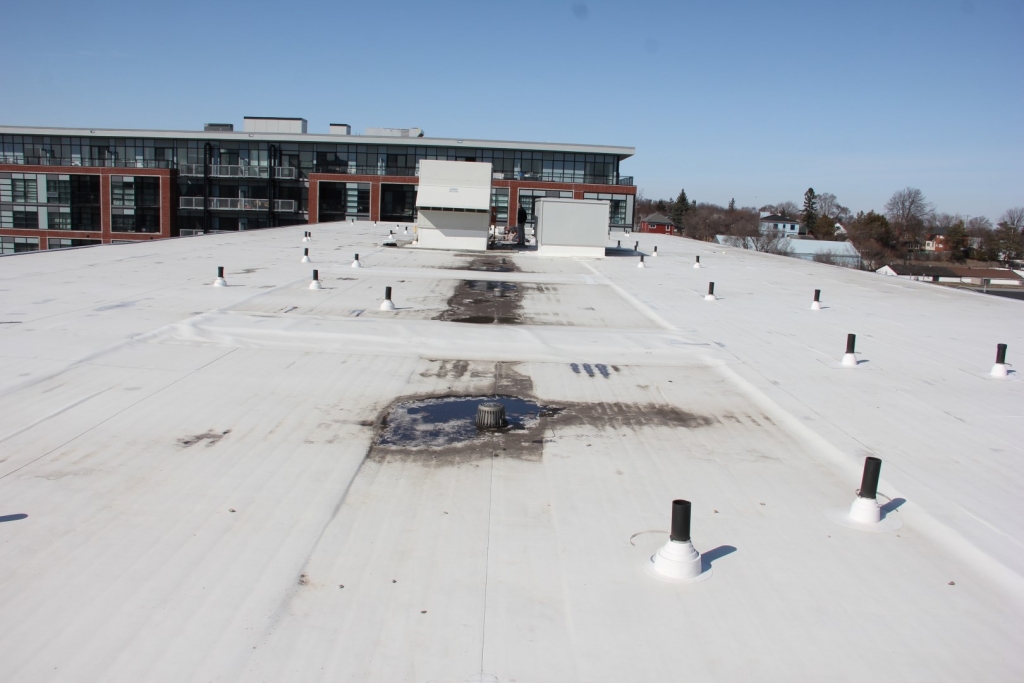
Unlike more traditional building construction which includes materials and assemblies which are more tolerant of periodic moisture exposure such as from roof leakage, this is a great example of a modern roof which is incredibly difficult to repair once damaged. Additionally, once leakage occurs (which is very likely at some point over the life of the building), it does a great job to conceal evidence of the leakage, allowing for more damage to occur before it is discovered. Ultimately, this roof can and will be fixed; however, any cost savings of originally constructing this roof assembly are likely to be exceeded during the repairs. There is also an environmental cost as a significant amount of the roofing materials will need to be disposed of after only five years in this case.